Intro
In 2014, I worked with Google’s robotics division to develop rugged, plastic skins for the Schaft robot. Schaft was originally engineered by a Tokyo-based robotics startup and won the DARPA robotics challenge. It was subsequently acquired by Google during Andy Rubin’s tenure as head of Google’s robotics division. Andy approached Speck Design (where I was working at the time) to image a more product-ready design for the robot.
I collaborated with a team of three industrial designers to bring a reimagined version of the robot to life. We had two main objectives:
- Develop a design language for the robot
- Engineer functional parts to skin the robot that incorporated the new design aesthetic
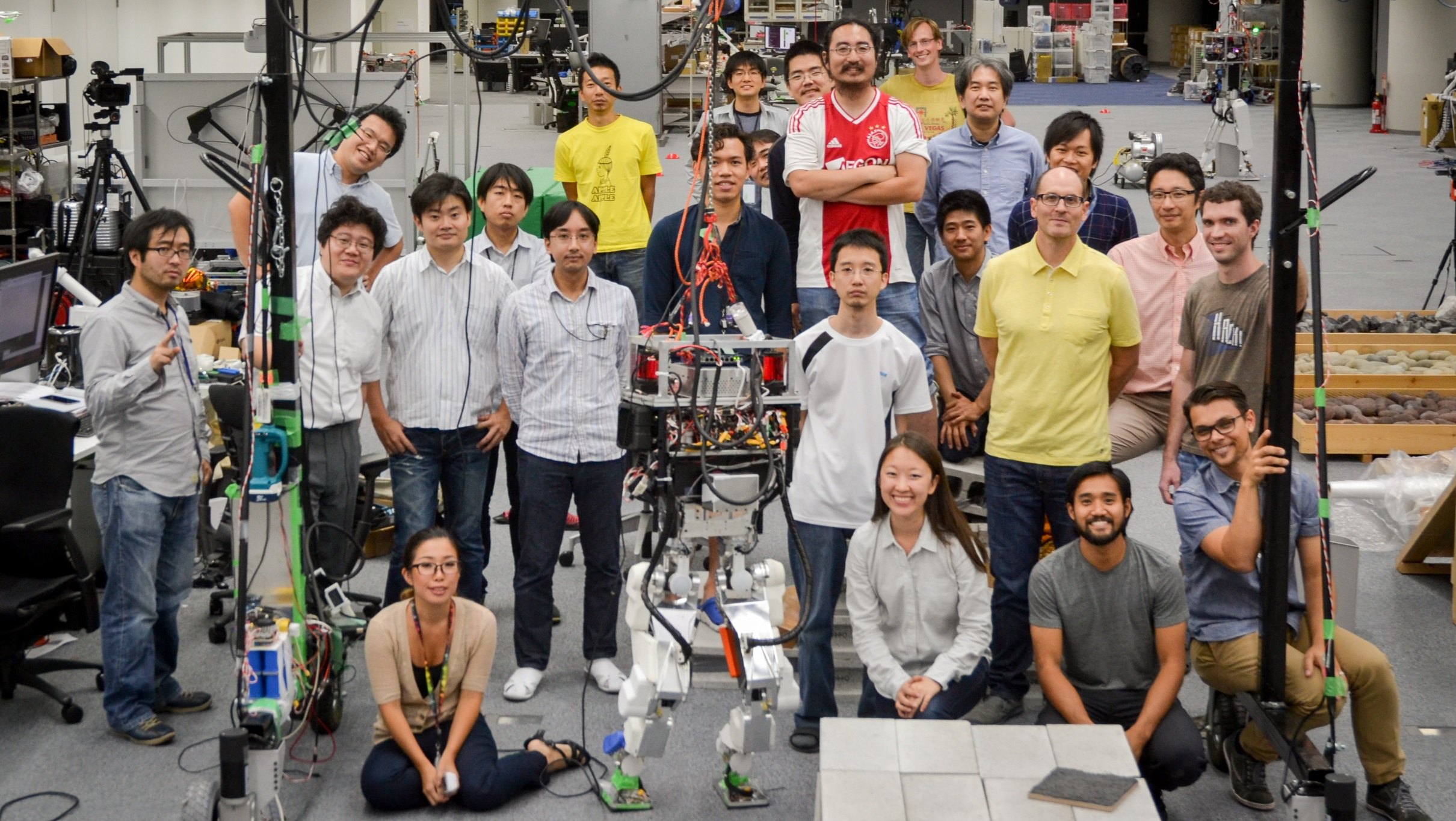
The Process
For this project, I spent an initial 2 weeks in Tokyo to gain a deep understanding of the robot’s mechanical architecture. I helped translate between the industrial designers and Google’s engineers to ensure that the design would not negatively affect functional performance of the robot. In particular, key consideration was given to thermal performance and joint range of motion.
The majority of the project required I work on the detailed part design without the physical robot in front of me. This necessitated thorough documentation on my part from my first trip to Tokyo. I then returned to Tokyo for another 2 weeks to conduct a fit check of the parts and to collaborate with the team for functional testing. Based on these results, I was able to finalize the physical part design and order the DVT model for demonstration to the broader Google team.

The Solution
The final deliverable incorporated the industrial design into physical parts that fit onto the robot’s chassis. I utilized a combination of rapid prototyping technologies to procure the parts. But each part was designed with a volume production method in mind (casting and CNC for metal, thermoforming for plastics).
Mechanical Design Highlights:
- Development of a robust, vibration resistant method for attaching the torso skins that required no visible fasteners (a key customer request)
- Engineering key contact locations between the contoured form and rectilinear metal chassis
- Improved design of chassis parts to increase resistance to axial and bending loads.
The Results
Ultimately, the Google team was very happy with the final design we delivered. In fact, the robot now sits in the lobby of Andy Rubin’s current company, Playground Global, in Palo Alto, CA.

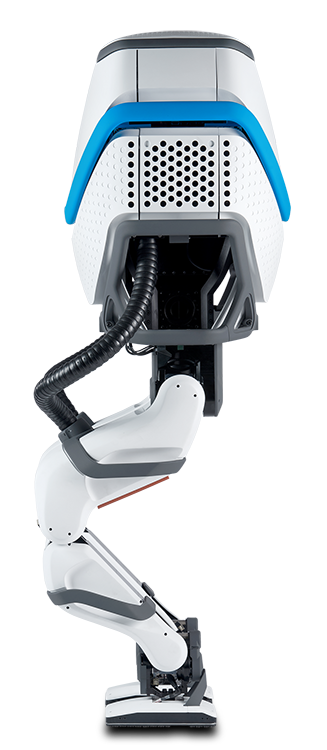
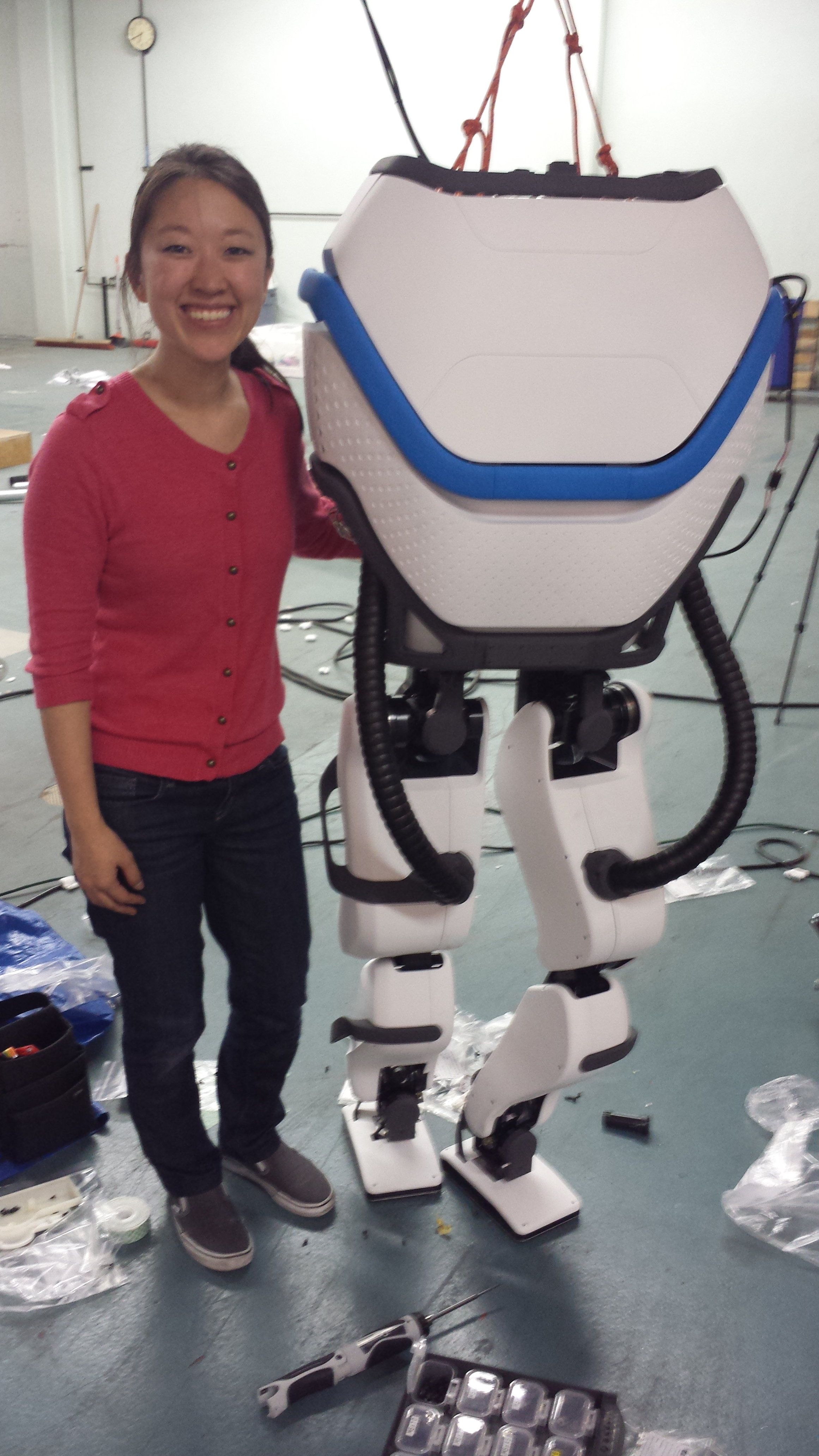